Honda HES 6501 test specification is comprised of many different types of testing to determine the adhesion and the coatings ability to resists corrosion. Honda HES 6501 test specification includes some of the following tests:
This is a visual check of the coating on the sample.
Used to determine the correct thickness of the coating applied to the sample.
Used to determine the correct thickness of the coating applied to the sample.
Used to measure the Specular gloss of the coating
Uses a light receiver specified in JIS Z 8722, and reporting according to JIS Z 8722.
This testing utilizes a special pencil sold by the Japan Inspection Association or a Mitsubishi Drawing Pencil UNI. The pencil is prepared per the Honda HES 6501 specification and force applied to the pencil as it is pushed forward at a 45° angle. The pencils are numbered according to the hardness. When a pencil causes a scratch that pencil number is recorded as the hardness.
Used to measure the adhesion of the coating. 100 equal squares are cut into the coating and cellophane tape is applied over this cut grid. The tape is pulled off at a 45° Angle. The number of squares that are removed and remained adhered is recorded.
The sample is prepared using abrasive papers and then the coating is applied. The finish is checked for wrinkles, craters, bleed, and pin holes.
Uses a DuPont impact tester to check for cracks and pealing of the coating after impact.
The coated panel is bent 180° within 1 second and is checked for cracks and pealing.
A sample is placed in a controlled temperature chamber with five layers of gauze and a weight placed on the center of the sample. After a set amount of time the gauze and weight are removed. The sample is checked to see if the cause adhered to the sample and if the gauze left any imprint on the sample.
The coated sample is rubbed with sandpaper specified in JIS R 6252 and the condition after is reported.
The sample is checked for appearance, color, and gloss after lightly rubbing the sample with gauze dipped in polishing agent.
This test is used to determine the corrosion resistance of the sample to salt spray testing in the same manner as ASTM B117 and JIS Z 2371. After the test is completed the x scribe is measured for the worst corrosion creep. This test can be conducted without the X scribe as well.
This test is used to determine the adhesion quality of coating applied to the sample. An X scribe is made on the test panel. The panel is exposed for 24 hours in a salt fog chamber and then placed in thermo-hygrostat chamber at 40°C for a set period of time. When testing is completed the filiform is measured from the scribe.
Paste as specified in Honda HES D6501 note #53 is applied to the sample 2-3mm thick. The sample is left in a thermo-hygrostat chamber at 50°C and 95% RH for 24 hours. After 24 hours the sample is rinsed off and inspected for rust, blisters, peeling, and other coating defects.
This test is used to determine the coatings resistance to water immersion.
The sample is placed in distilled water at 40°C for a set period of time. After testing the sample is checked for wrinkles, blisters, peeling, etc. The sample will undergo a cross hatch test with two hours of removal from the water.
This test is used to determine the effects of humidity on the sample coating.
The sample is exposed to 50°C/95% RH for a specified amount of time. The sample will undergo a cross hatch test with two hours of removal from the water.
The test sample is exposed to a determined temperature for a specified amount of time. After completion the sample is checked for adhesion, corrosion resistance, past resistance, volatile solution resistance, and wear resistance.
The sample is heated to a specified temperature and then rapidly cooled using cool water. Sample is then checked for defects.
This test checks the coatings ability to withstand volatile solution.
The sample is placed in a glass container with the volatile solution covering ½ to 2/3 of the sample for a set period of time. Sample is then checked for defects.
Xylene conforming to JIS K 2435 is applied to ten layers of gauze and the sampled rubbed eight times. Sample is then checked for defects.
This test checks the coatings ability to withstand oil. The sample is placed in a glass container with the oil covering ½ to 2/3 of the sample for a set period of time. Sample is then checked for defects.
This test checks the coatings ability to withstand Alkali. The sample is placed in a glass container with the sodium hydroxide covering ½ to 2/3 of the sample for a set period of time. After immersing the sample, it is rinsed with clear running water. Sample is then checked for defects.
This test checks the coatings ability to withstand acid. The sample is placed in a glass container with the sulfuric acid covering ½ to 2/3 of the sample for a set period of time. After immersing the sample, it is rinsed with clear running water. Sample is then checked for defects.
This test checks the coatings ability to withstand sweat. The sample is placed in a glass container with the synthetic sweat covering the sample for a set period of time. Sample is then checked for defects.
This test checks the coatings ability to withstand detergent. The sample is placed in a glass container with the detergent solution specified in JIS K 3371 covering the sample for a set period of time. Sample is checked for defects.
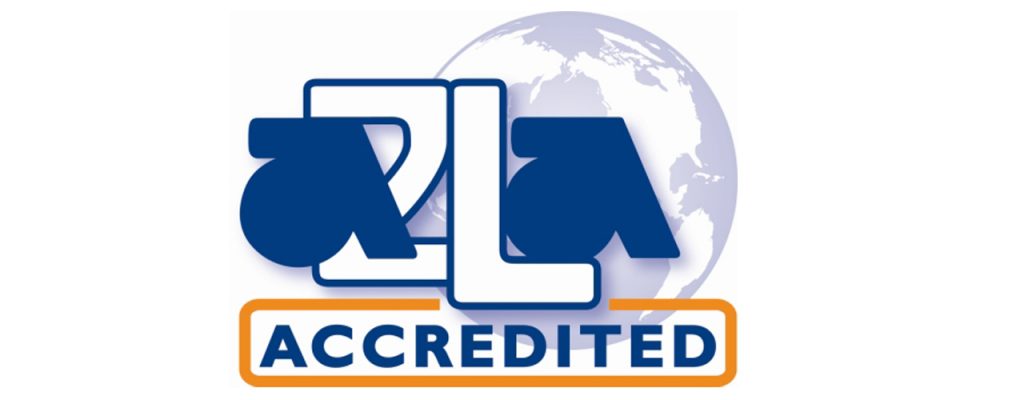
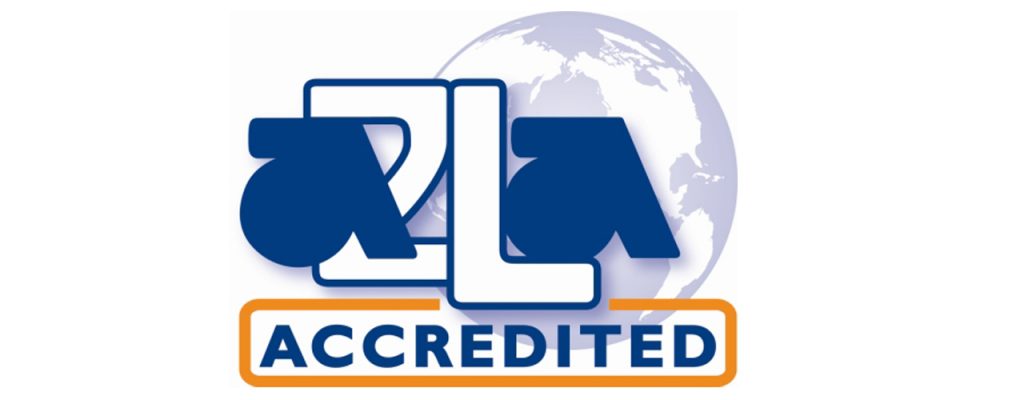
Testing Certificate # 2563.02
Our lab is accredited by A2LA.Scope
A2LA Letter of Accreditation (PDF)
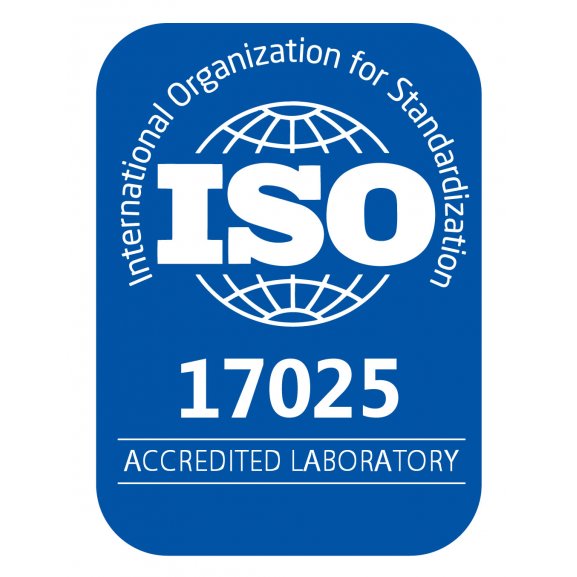
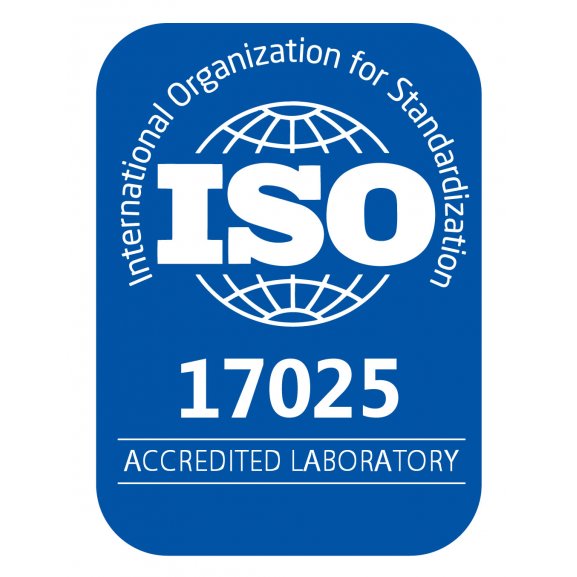
Benefits of ATC Test Lab
A2LA Accredited Test Lab
Many manufacturers want to avoid hiring a certified professional to conduct their sophisticated testing. By contracting ATC Test Lab you can avoid hiring and training costly specialized employees and equipment to conduct an array of tests.
Our experienced laboratory technicians understand the nature of each test, including Honda HES 6501. They are able to quickly detect product failure or unusual corrosion.
Specialized Testing Equipment and Chambers
ATC has new state of the art equipment to perform the most advanced testing. We have over 1200 Cubic Feet of testing space available, and the largest testing chambers in the world.
By contracting us, you can save money on new costly equipment, maintenance, and down time. You can size and scale your tests based on your level of production.
Receive Photographs and Updates
The best way to monitor your products during the testing process is though digital photography. ATC Test Lab offers high resolution photos at your requested intervals. The use of photographs can help you save money if you need to stop the test early due to product failure or unusual corrosion.
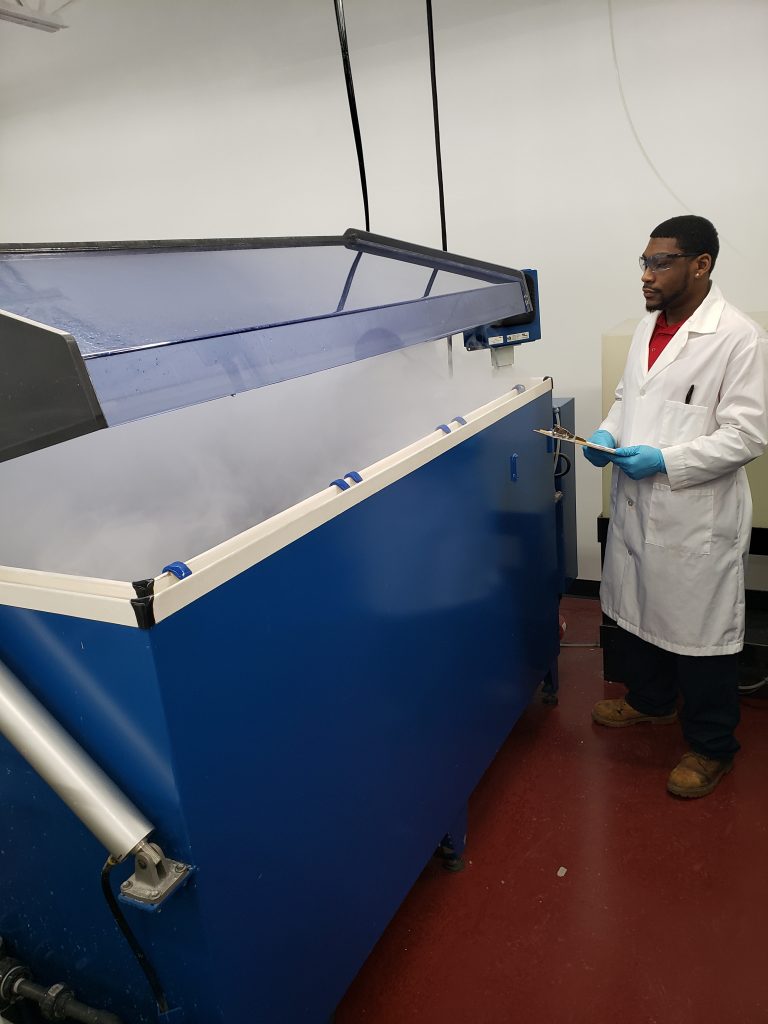
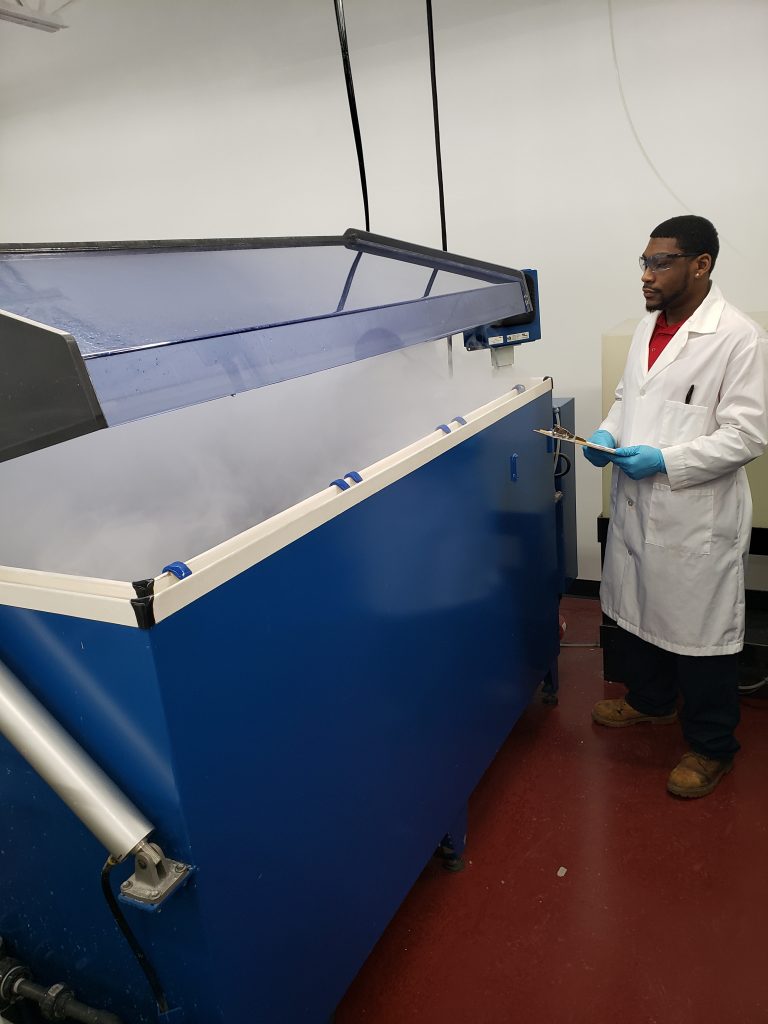
Toyota TSH1552G Testing being conducted at ATC Test Lab
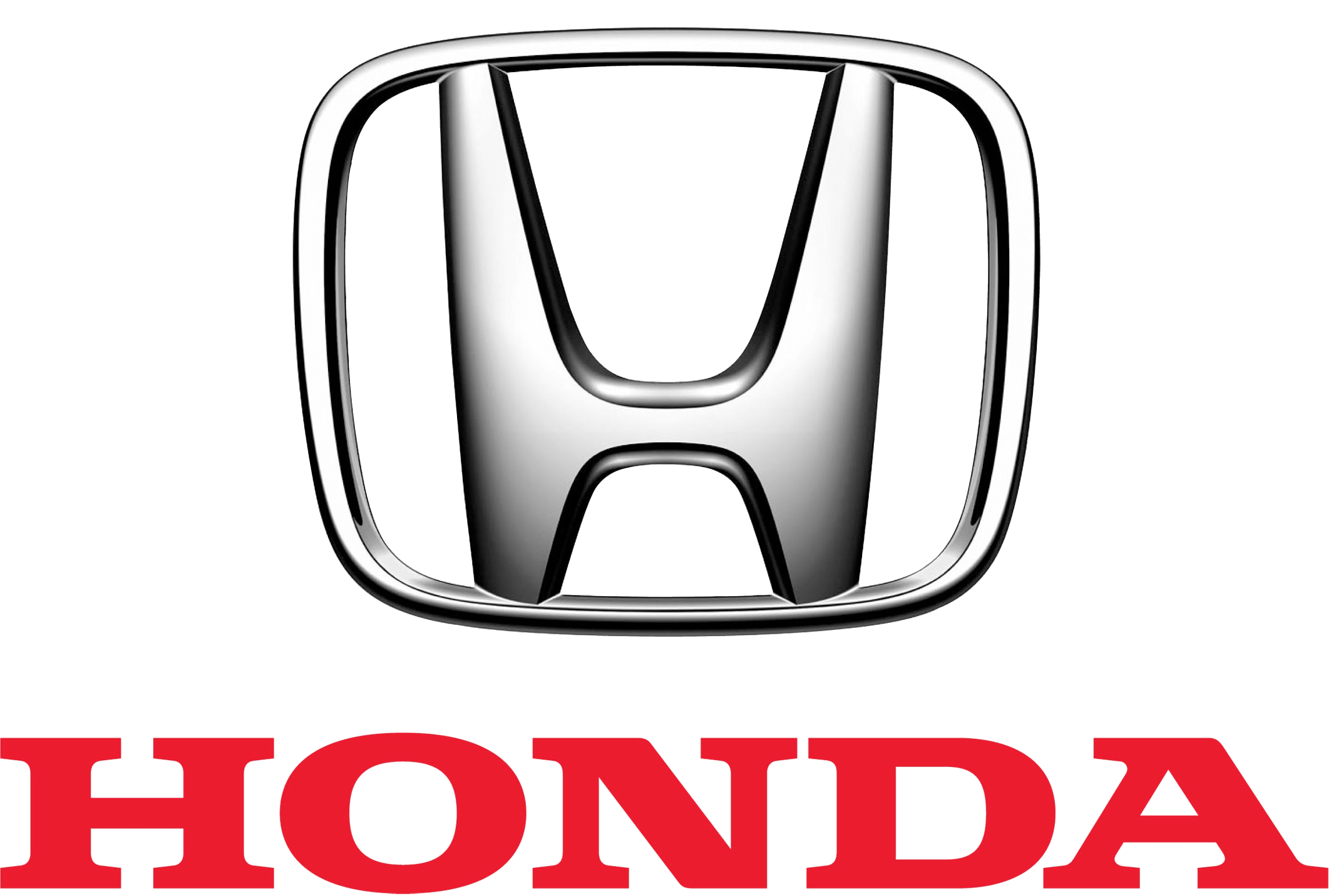
Honda HES 6501
General Test Method for Coating
Salt Fog Testing Chamber
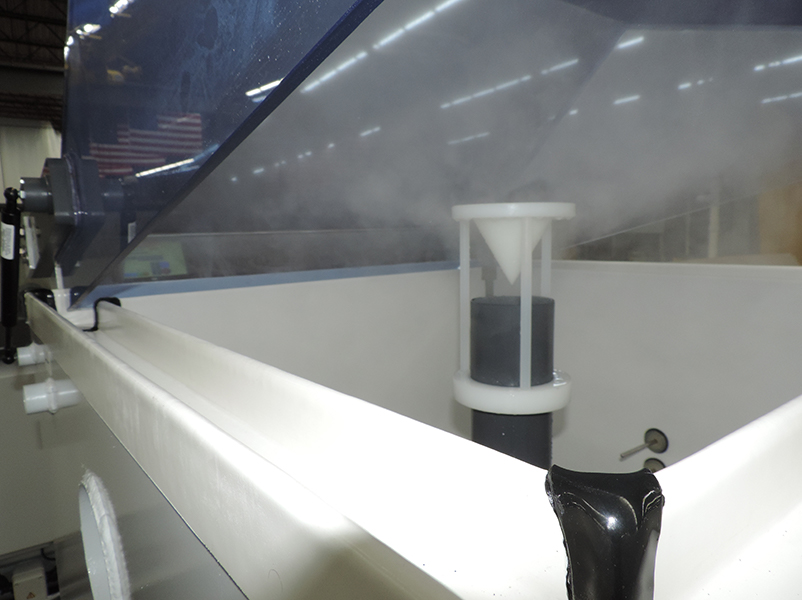
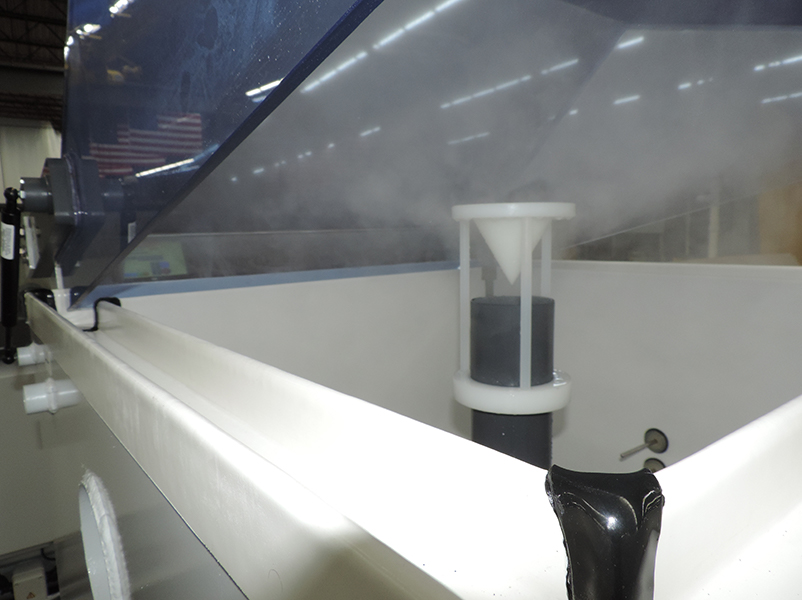
ATC Test Lab is the Largest Contract Corrosion Test Lab.
- We have over 1200 cubic feet of testing space available.
- Large testing chambers
- Our lab has state of the art equipment to perform the most advanced testing.
- Experienced laboratory technicians conducting your tests.